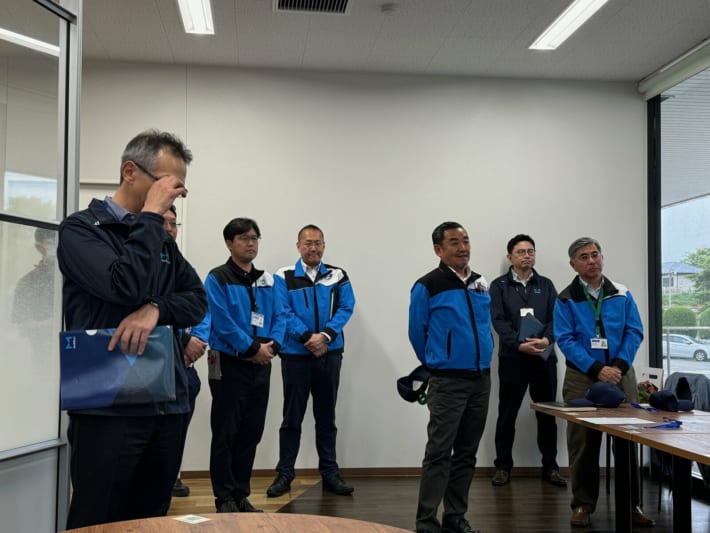
2024年4月、グローバル・サプライヤーのMARELLI(マレリ)は、AJAJ会員向けに勉強会を開催した。と同時に経産省の自動車産業室の方や、埼玉県産業労働部の方、埼玉県産業振興公社の次世代モビリティセンターの技術開発支援グループの方も参加され、埼玉県吉見町にあるマレリを視察した。
カルソニック・カンセイからマレリへ
マレリは2023年7月にインテリア部門の全てが、この吉見町に集約され、2024年3月にインテリア・イノベーションセンターを設立している。
マレリの沿革は、1925年関東精器と蜂巣工業所をルーツに持ち、社名変更や吸収合併などを経て、カルソニック・カンセイとなり、インテリアやラジエター製品などのTier1として活動していた。そして2018年にイタリアのグローバル・サプライヤーであるマニエッティ・マレリを買収し、2019年にマレリへと社名変更しているグローバルサプライヤーだ。
この吉見工場は96%がインテリア部品を製造している工場で、日産車を対象としたものが多く、他にホンダ、トヨタ、そしてUDトラックといったOEMが取引先という説明だった。
マレリのインテリア部門を埼玉県吉見町に集約した狙いは、「異なる専門家が集まってイノベーションを作り出す」がひとつある。そしてデジタル環境の中であっても、机上の空論ではなく現場で現物を認識する三現主義に基づき、イノベーションを作り出せる環境づくりとツール作りを目指すこと。さらに、世界初や日本初を多く輩出した歴史の延長で、夢や妄想をいかにスピーディに実現するかというマインドセットを持てるようにする、という狙いを持っているとインテリア・エクスペリエンス事業本部の成富光義氏から説明があった。
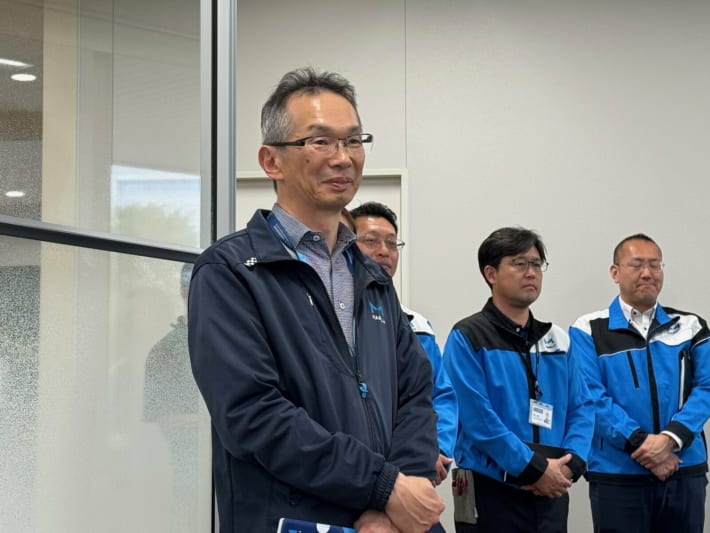
IICからOEMへの提案
そうした狙いを踏まえてインテリア・イノベーションセンター(IIC)内のラボの見学と実際の製品を製造する工場を見学することができた。
IICでは、OEMへの提案や実際に納品している製品などの展示物を見ながら、エンジニアたちの説明を個々に聞くことができた。そのため、AJAJ会員個人が興味を持てる分野に集中でき、見識を広げられる見学方式だった。
ここでのポイントは、ひとつにはサスティナビリティが求められる現在、素材開発においてリサイクル、リユースといった素材を使った製品が求められていること。そして、VRを使って実際の走行でどんなレイアウトのダッシュボードが良いのか、どんなスイッチがいいのか、視認性はどうかといったデジタルツイン技術を用いた開発をすること。
さらに、光と素材の組み合わせでゆらぐ光やスピードを感じさせる演出、リラックスできる光など、人間の感性に響くマルチモーダルへ結びつく技術を開発し、OEMへ提案していくことなどがあった。そして現在開発しているもの、求められているものとしてHMIのコックピット開発がある。そして自宅リビングとシームレスにつながることも重要と位置付けている。
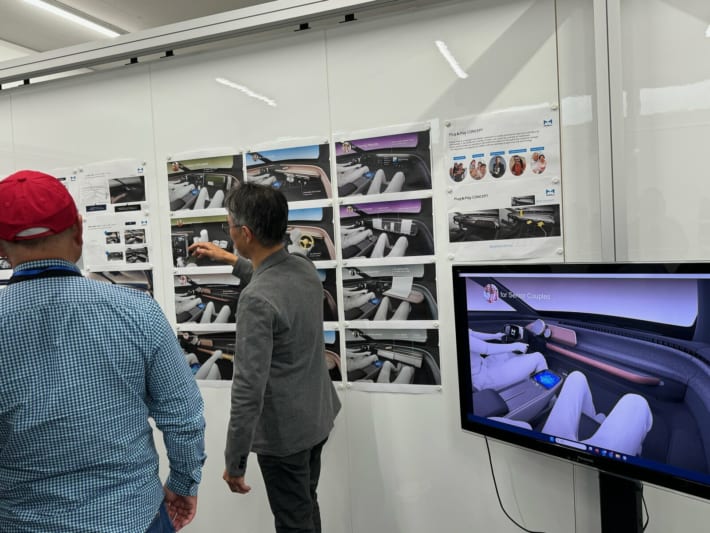
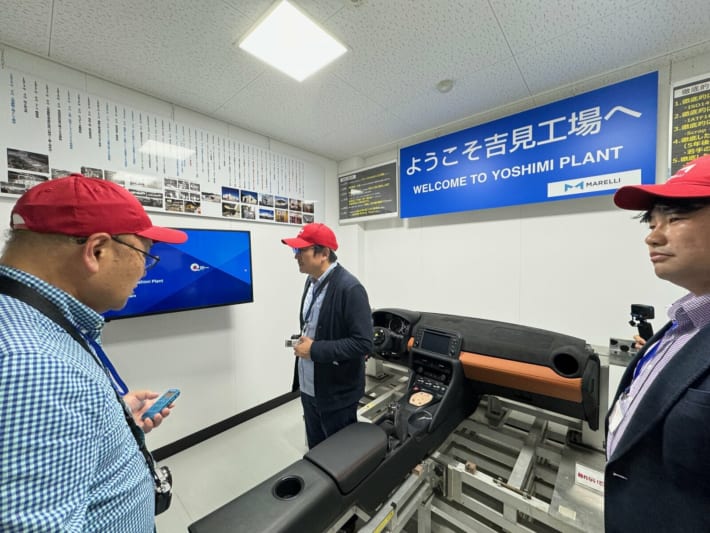
必要なものだけを表示するデジタル・デトックス・コックピット
ここでは、デトックスという言葉が用いられて説明を受けたが、デジタル化、コネクテッド化、技術の高度化などにより、ありとあらゆることが車内でできるようになり、現在地としては情報が溢れている状況だ。そこを、本当に必要なものか?といった視点を盛り込んだ「デジタル・デトックス・コックピット」を体験させてもらえた。
必要なものはわかりやすく、不要なものは隠すことが必要だと説明された。が、必要、不必要の判断はどこで行なうのか?伺うと「遭遇するシーンで必要なものが決まることと、もうひとつは、個人差があり精神的なもの、空間から受ける感性みたいなものがあるので、その2点がポイントになります。そして個人差に関してはドライビング・シミュレーターを使って、日夜人間の構造研究を進めています」という回答を得た。
一方で、ドライバーアバターを作り、行動学習をすることでクラウドに情報を集約し、必要なシーンに合わせて対応するという方法も研究しているということも伺えた。
このようにHMIコクピットは各社開発競争が激しく、また中国市場、北米、欧州、そして日本でもその要求内容が異なる複雑さも持っているため、コストを踏まえた製品開発がこのインテリア・イノベーションセンターで行なわれていることが理解できた。
職人技が求められる製造工程
後半は実際の製品を作る工場見学をした。最初に見学したのは塗装工程で、特徴は自己修復機能を持つ塗装でピアノブラックに塗装された部分に擦り傷がついた場合、自然と擦り傷が消えていく塗装。これは塗料が柔らかいことで、凹みが自然回復する性質を利用したものだ。
次にバルクヘッドと呼ぶフレーム製造工程で、ラジエターやヘッドライト、コンデンサー等をフロントに取り付ける際のフレーム。こちらはホンダへ納品しているという説明だった。
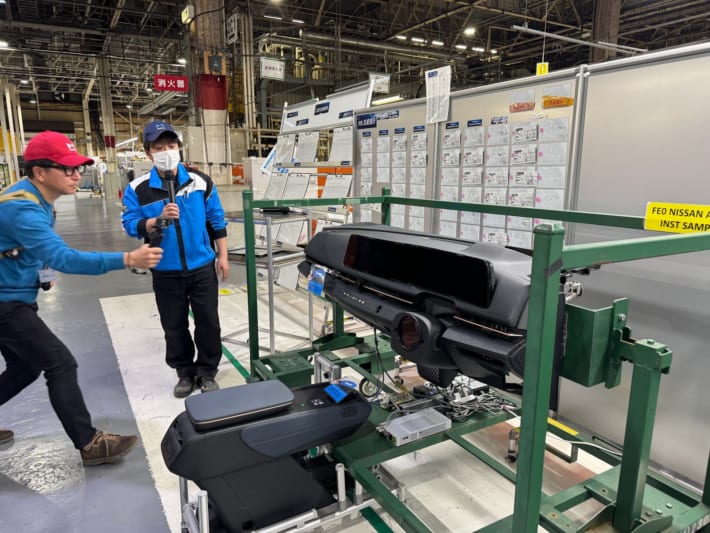
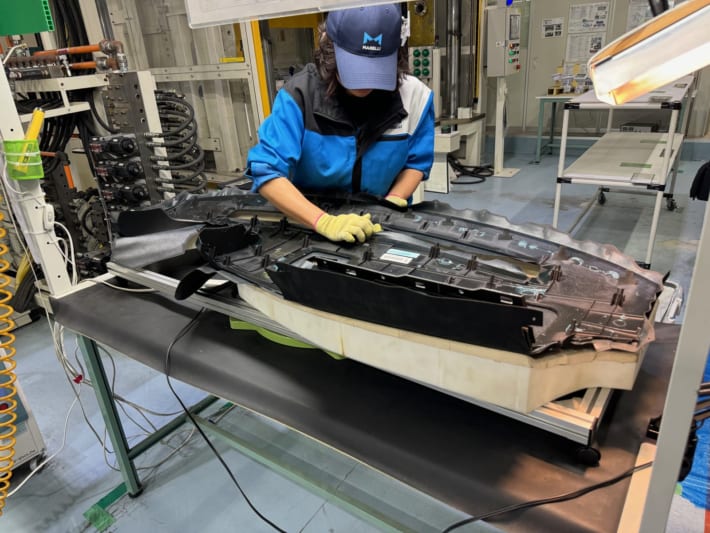
興味深いのはIICでもサンプル展示されていたが、スマートサーフェイスという部品で、パネルの裏側に電子部品を仕込み、タッチ操作をした際、スイッチからのフィードバックが得られるものだ。これはiPhoneにある「触覚タッチ」のことでハプティック・タッチという機能を持たせたパネルを製造していた。
驚いたのは、これだけ自動化が進む中でも、人の手により職人技が必要な部品があることだった。GT-Rのダッシュボードにレザーを貼る工程で、表皮はグレードにより3パターンあり、本革、アルカンターラ、合皮で、それぞれを職人が丁寧に貼る作業を見学した。
GT-Rのようなスペシャルな車両にはこうした職人技が盛り込まれているほうが高い付加価値があるというわけだ。
工場見学を終え、同行見学された役人の方々からは、AJAJ会員の質問の鋭さに驚くととともに、改めて自動車ジャーナリストという確立された専門家集団を持っている自動車産業への認識を新たにした。というコメントを頂いて閉会した。
■参加者(18名) |
---|
会田肇/有元正存/石川真禱照/菰田潔/斎藤聡/鈴木直也/清水和夫/高山正寛/高橋アキラ/近田茂/南陽一浩/西村直人/松田秀士/森川オサム/諸星陽一/山崎元裕/吉田由美 |