2月19日、神奈川県にあるバッテリーメーカー大手AESCジャパン座間工場にて、AJAJバッテリー勉強会が開催された。
現在も日産自動車が一部資本を保有するバッテリーメーカーとして、生産能力をこの数年間で約10倍もの規模に拡大するという意欲的な計画を発表し、世界的な大手の一角に参入すべく名乗りを上げた企業である。
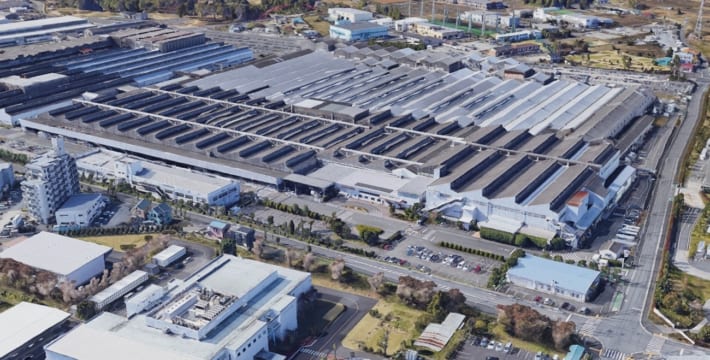
当日は、AESCジャパン 代表取締役社長兼CEOの松本昌一氏をはじめ、役員の方々も参加し、和やかな雰囲気のなかで座学から勉強会はスタートした。
■特徴的なグローバル多拠点展開
AESCジャパンは、日産や三菱、ホンダのEV向けのパウチ型バッテリーセルを製造しているメーカーとして知られる大手バッテリーサプライヤーだ。
AESCはもともと、日産自動車とNECとの合弁企業として2007年に設立され、2019年には風力発電用タービンのトップシェアメーカーである中国エンビジョン・エナジーの出資を受け、現在は同社が9割弱、日産自動車が11.8%のシェアを保有している。
AESCジャパン 代表取締役社長兼CEOの松本昌一氏は、同社の現在と今後の展望について語った。
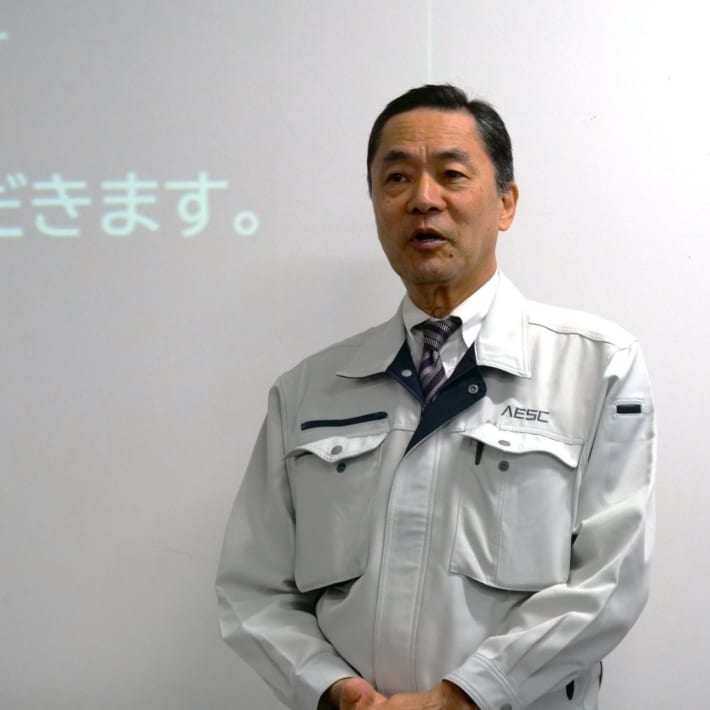
「私たちはカーボンニュートラルな社会の実現を目指し、EV(電気自動車)向けを中心にバッテリーの生産・販売を行っています。AESCは2010年に日産リーフ向けのバッテリー供給を開始して以来、世界6カ国で生産拠点を展開してきました。この17年間、バッテリーに起因する発火事故は一切発生していません。これは日本のものづくりの強みを示す証拠です。」
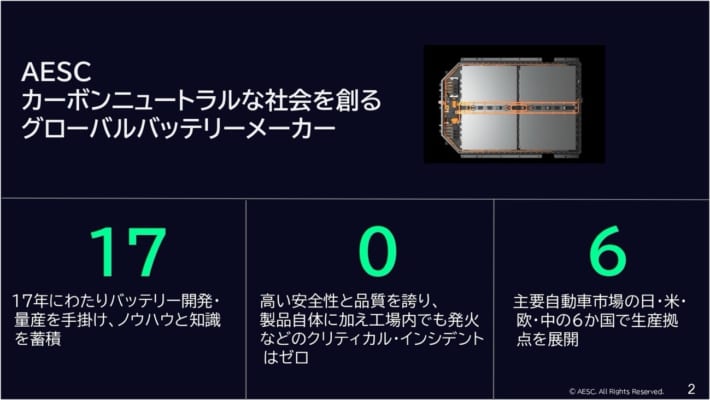
現在、AESCは日本・米国・欧州・中国の6カ国で生産拠点を構築。特に、ギガファクトリーの建設が進行中である。
「新たに7つのギガファクトリーを建設中です。日本の茨城工場はすでにホンダ向けのバッテリー生産を開始し、日産向けも試作段階に入っています。アメリカではケンタッキー州のボウリンググリーン工場がメルセデス・ベンツ向け、サウスカロライナ州のフローレンス工場がBMW向けに準備を進めています。イギリスのサンダーランド工場では、日産およびジャガー・ランドローバー向けの生産が計画され、フランスのルノー工場隣接地にも新工場を建設中。スペインのエストレマドゥーラでは50度を超える砂漠地帯に新工場が立ち上がります。」
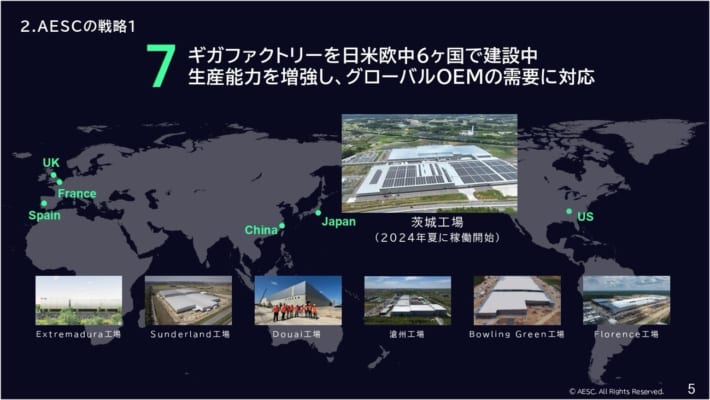
中国では既存の無錫、オルドス、十堰に加え、天津南部の滄州にも新工場が建設される。
「地産地消の促進が重要です。バッテリーの材料であるニッケル、コバルト、リチウムは世界各地から調達しますが、アメリカ市場では中国を除いた供給源を確保するなど、各地域の事情に応じたサプライチェーンを構築しています。また、リサイクルにも力を入れており、日本・中国・米国・欧州で使用済みバッテリーからリチウムやコバルトを回収し、再利用する取り組みを進めています。」
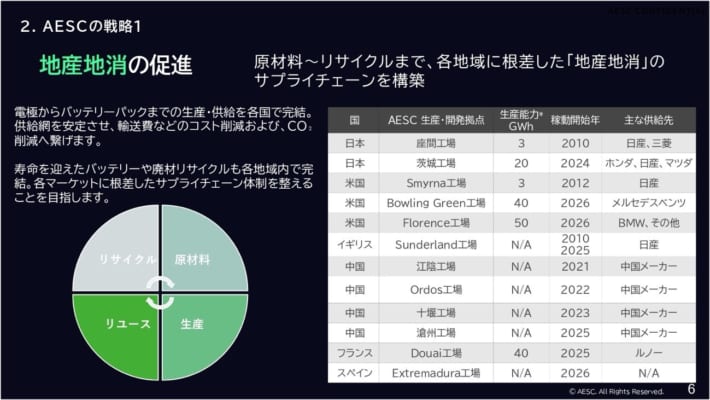
AESCの生産能力は今後大幅に増強される見込みだ。
「現在、世界の生産能力は20〜30GWhですが、2026〜2027年には200〜300GWhへ拡大します。特に、アメリカのボウリンググリーンとフローレンス工場はそれぞれ40〜50GWhの規模を誇ります。フランスのドゥエイ工場も40GWhで、大規模な供給体制が整います。」
■NMCだけでなくLFPも 全固体電池まで手掛ける
また、AESCのバッテリー技術も進化を続ける。
「当社のバッテリーは、NMC(ニッケル・マンガン・コバルト)とLFP(リン酸鉄リチウム)の2種類を展開しています。NMCはエネルギー密度が高く高級車向け、LFPはコストが安く大衆車や定置向けに適しています。さらに、パウチ型、缶型、円筒型といった異なる形状のバッテリーを揃え、用途ごとに最適なソリューションを提供しています。テスラが円筒型を1000本以上使用するのに対し、当社のパウチ型は200〜300個で済むため、設計の柔軟性が高いのが特長です。」
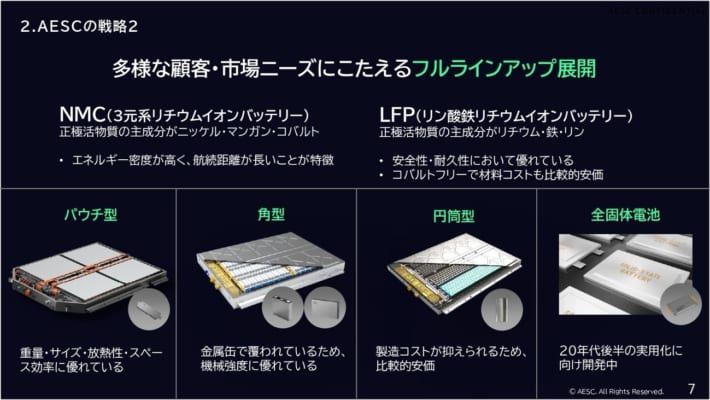
全固体電池の開発も進行中で、20年代後半の実用化を目指している。
「全固体電池はエネルギー密度が従来の1.5倍以上となり、高級車やスポーツカー向けに適しています。急速充電性能も向上し、ジェネレーション6・7では10分以内の充電が可能になります。」
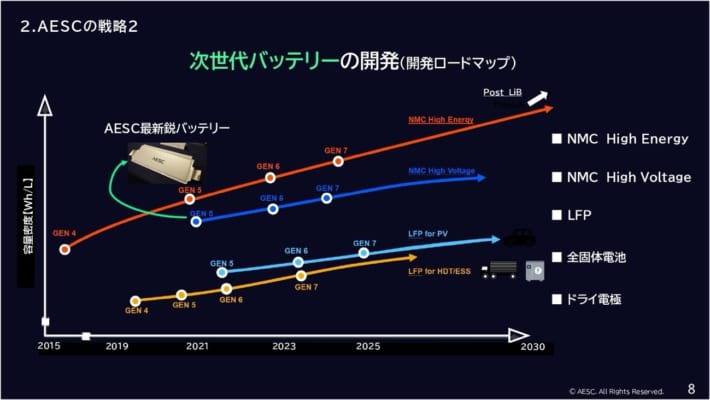
環境負荷の低減にも取り組んでいる。
「EV生産時のCO2排出を削減するため、茨城工場では屋根にソーラーパネルを設置し、電力の15%を再生可能エネルギーで賄います。さらに、海外拠点でも風力発電や太陽光発電を活用し、クリーンエネルギーの利用を拡大しています。」
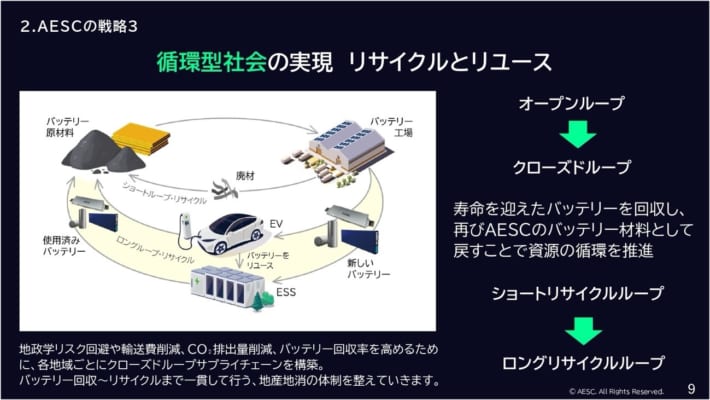
国内生産拠点も拡充される。
「座間工場では1000名の従業員がリーフやアウトランダー向けのバッテリーを生産。相模原工場は電極の生産を担当。茨城工場は第5世代バッテリーのグローバル拠点として、2025年度末には2000名規模の従業員を抱える見込みです。生産能力も6〜7GWhから20GWhへ拡張可能で、日本のマザー工場として機能します。」
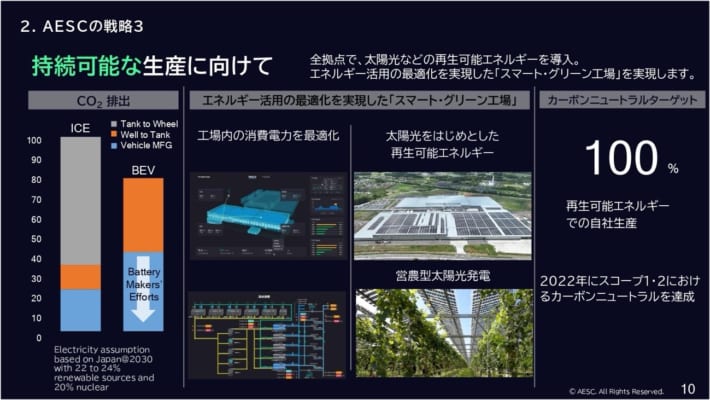
AESCの取り組みは、世界の電動化を加速させる重要な役割を担っている。今後のさらなる成長が期待される。
つづいて、AESCジャパン 経営企画部 常務執行役員の野田俊治氏は、グローバルなEVトレンドの変化とバッテリー需要の予測について語った。
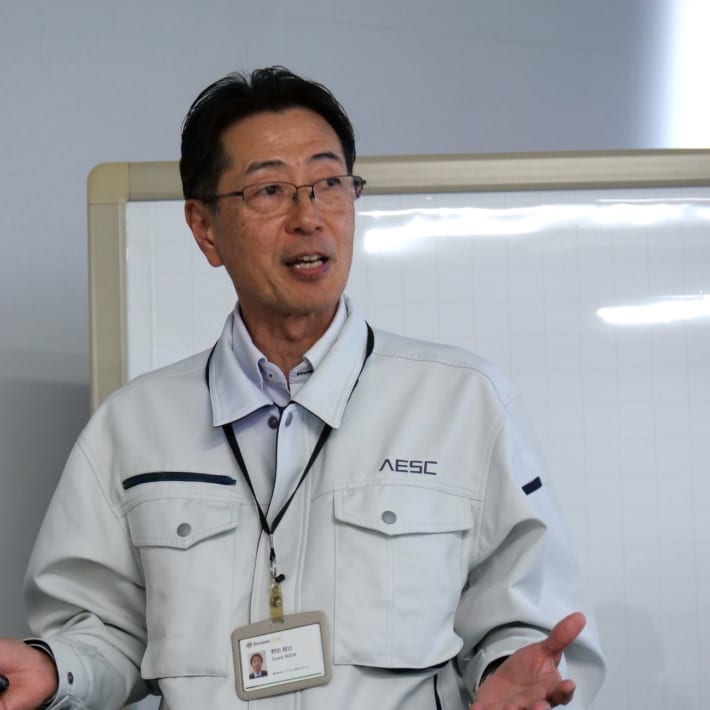
「現在、世界各国が2050年までのカーボンニュートラル達成を掲げています。日本は2035年までに電動車販売比率100%を目標としており、アメリカは2030年までに50%、ヨーロッパやイギリスは2035年までに100%の電動化を計画してます。中国も2027年には新エネルギー車比率を45%に引き上げる方針です」
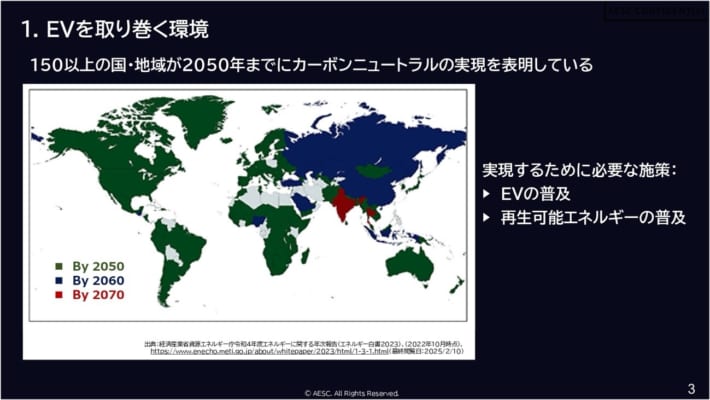
こうした政策に呼応し、多くの自動車メーカーは2050年までのカーボンニュートラルを宣言し、内燃機関の開発・投資の停止を決定している。
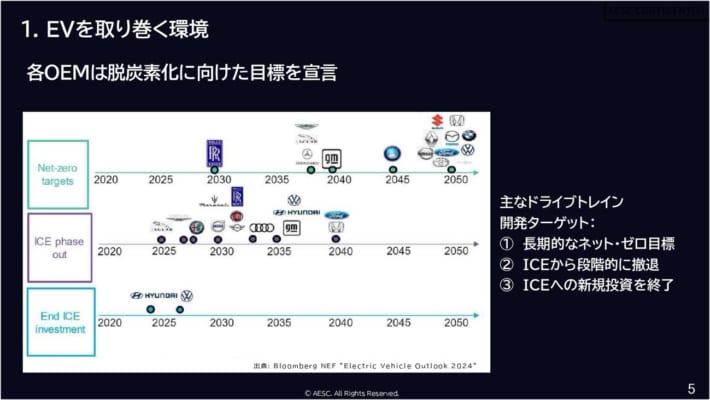
■EV市場の新たな課題
EV市場の成長トレンドは、変化しながらも続いていくと予測されている。しかし野田氏は「EV市場の成長にはサプライチェーンの偏りというリスクがある」と指摘する。
特にバッテリーの主要材料であるコバルトはコンゴ民主共和国、グラファイトは中国に大きく依存しており、地政学的リスクが高い。
「例えば、中国がグラファイトの輸出を制限すれば、世界のEV生産に深刻な影響を与えるでしょう」と述べ、各国が自国のサプライチェーン強化を進める必要性を強調した。
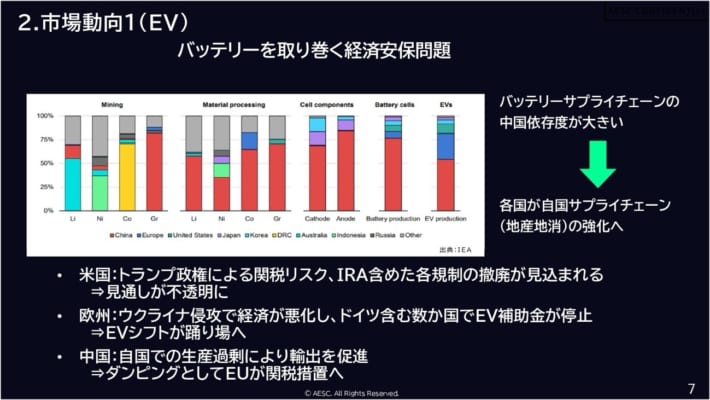
また、アメリカではトランプ政権の政策変更が影響を及ぼす可能性がある。
「トランプ前大統領は自動車への関税を25%に引き上げることを検討しており、IRA(インフレ抑制法)の撤廃も議論されています。非常に不透明な状況です」
一方、ヨーロッパではウクライナ紛争による電力価格の高騰とEV補助金の廃止が市場の伸びを鈍化させている。特にドイツでは2023年の補助金廃止後、市場の成長が停滞している。
■中国の生産過剰と市場への影響
いっぽう中国ではEVおよびバッテリーの生産能力が過剰になっている。
「中国はすでに国内需要を上回る生産能力を持ち、現在はヨーロッパや日本への輸出を加速せざるを得ない状況になっています。この動きに対し、ヨーロッパは中国製EVに対する反ダンピング措置を検討しています」
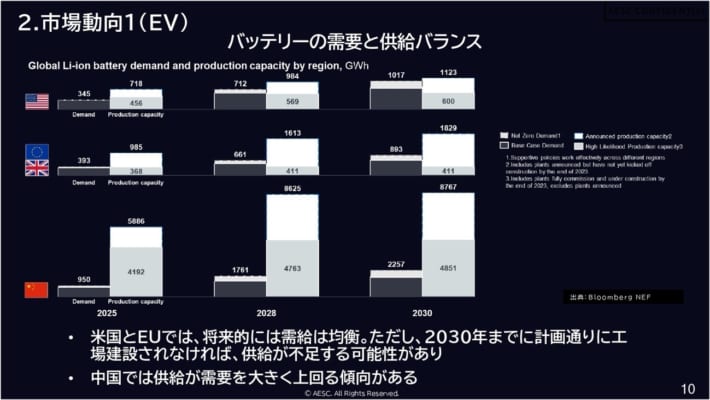
市場の変化に伴い、プラグインハイブリッド車(PHEV)の成長も顕著になっていると野田氏は指摘する。
「EVの伸びが2022年の69%から2024年には6%にまで鈍化する中、PHEVは燃費の良さや充電インフラの制約を受けないメリットから、引き続き成長しています。特に中国では需要が拡大しています。」
バッテリー技術ではLFP(リン酸鉄リチウム)バッテリーの優位性が高まっている。
「LFPは、エネルギー密度はNMC(ニッケル・マンガン・コバルト)バッテリーに劣りますが、コストが低く、寿命が長いため、コンパクトカーからB・Cセグメント車まで幅広く採用されています。LFPの技術革新により、さらに高密度化が進んでいることもそれを後押ししています」
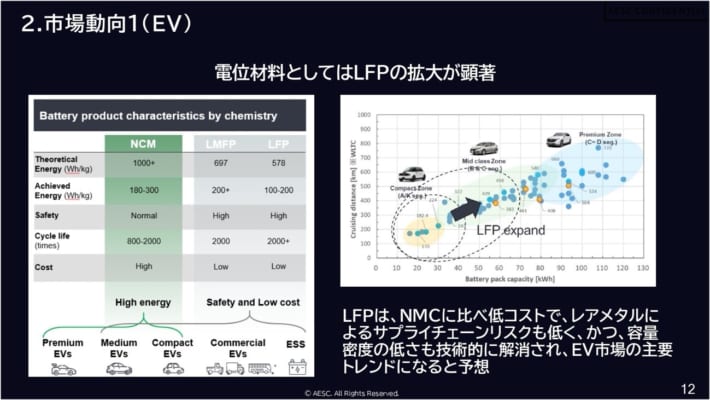
■ESS市場の拡大とバッテリー需要の将来
また、定置型蓄電システム(ESS)の需要拡大も予測される。
「世界的にAIとデータセンターが急成長し、この電力消費量は2026年に1000TWhを超える見込みで、これは日本の年間電力消費量に匹敵します。データセンターの24時間稼働を支えるため、再生可能エネルギーと併用した大規模な蓄電池の導入が求められています」
「それに伴い2030年にはESS向け蓄電池市場は年間2200GWhに達すると見込まれます。バッテリー産業は今後も成長を続けるでしょう」と野田氏は結論付ける。
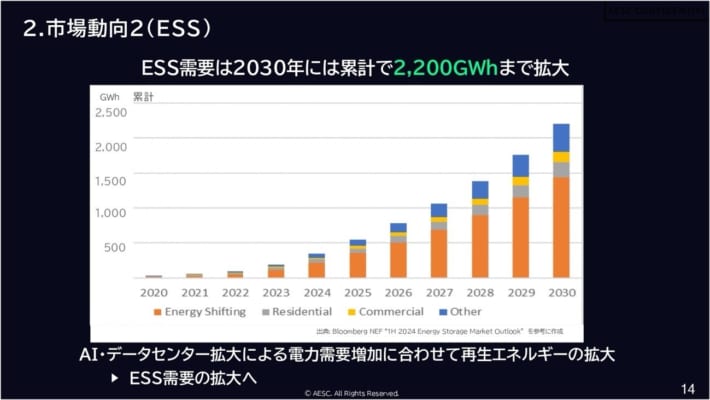
AESCジャパンはこの市場動向を見極め、戦略的にバッテリー供給を行っていく構えだ。
つづいて、AESCジャパンCTOの明石寛之氏は、バッテリー技術の進化と将来の展望について、AESCの視点から解説した。
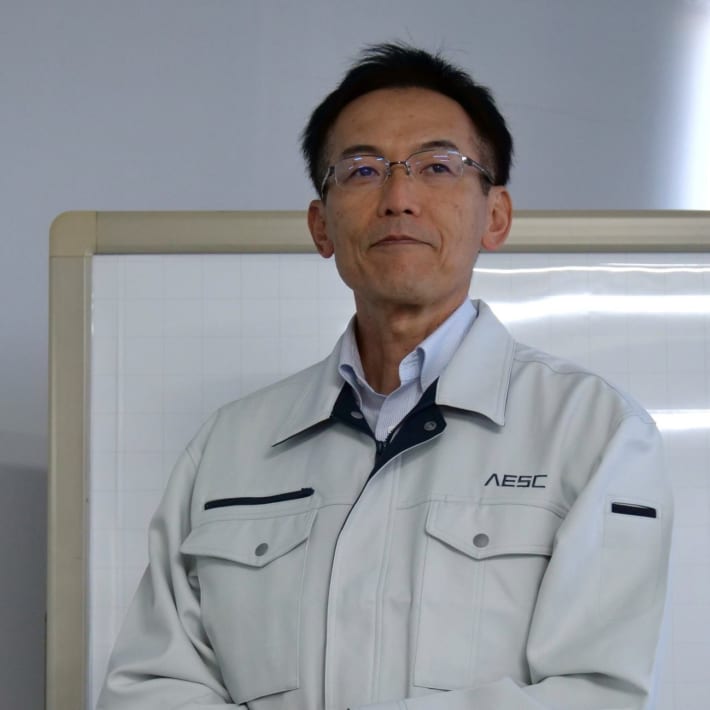
■バッテリーの基本構成と進化
バッテリーは、バッテリーパック、モジュール、セル、電極、そしてそれを構成する材料から成り立っている。この中でも、電池の性能を決定づけるのはセルの構造であり、特に「正極・負極の材料や、電解質の進化がリチウムイオンバッテリーの発展を支えてきた」と明石CTOは強調する。
バッテリーの歴史を振り返ると、1990年にニッケル水素電池が登場し、その翌年の1991年にソニーがリチウムイオンバッテリーを開発した。この時点では両者のエネルギー密度に大きな差はなかったが、「リチウムイオンの伸びしろは圧倒的で、エネルギー密度が2倍、3倍、4倍と急速に向上することになりました」と明石CTOは指摘する。これにより、リチウムイオンバッテリーは自動車用電池の主流へと成長した。
■HEV・PHEV・EVの違いとバッテリー設計
ハイブリッド車(HEV)、PHEV、EVはそれぞれ異なるバッテリー設計を必要とするという。
「EVは大容量のバッテリーを搭載し、それをゆっくりと消費していくが、HEVは小型のバッテリーを搭載し、瞬時にエネルギーを放出する必要があります。そのため、小型で瞬発性の高いバッテリーが求められます」と明石CTOは説明する。
PHEVはEVとHEVの中間的な特性を持つが、近年はEV寄りのバッテリー設計が進んでいる。
「中国では40kWh級のバッテリーを搭載したPHEVが登場し、BEVとの差が小さくなっています」との見解を示した。
■LFP vs NMC どちらが主流になるのか
バッテリーの正極材料には、LFP(リン酸鉄リチウム)とNMC(ニッケル・マンガン・コバルト酸リチウム)の2つの主要な選択肢がある。
「NMCは、エネルギー密度がLFPの1.7倍高いのですが、コストも高くなります。一方、LFPは安価ですが重量が重く、エネルギー密度が低い。中国ではLFPの最適化が進み、400km走行可能なEVも登場しています」と明石CTOは分析する。
ただ今後については、LFPはすでに技術的な伸びしろが少ないいっぽう、NMCにはまだ22%の性能向上の余地があると明石氏は見る。「最終的にはNMCとLFPがうまく棲み分けていくでしょう」との見解を示した。
■全固体電池の現状と課題
次世代バッテリーとして注目される全固体電池について、明石CTOは慎重な姿勢を示す。
「現在、各メーカーが開発を進める全固体電池の性能目標は、全体的に下方修正気味であります。いっぽうで液系電池の性能や使い勝手は進化しており、全固体電池は高性能な製品でないと市場に受け入れられないでしょう。リチウムイオンと同等の性能では存在価値が問われることになります」と述べる。
また、バッテリーの製造工程についても、「全固体電池の課題である寿命やコストの問題に見通しをつけない限り、いきなり大規模な工場建設には踏み切れないでしょう」と指摘する。
いっぽうで、急速充電性能が注目されるなか、バッテリーの劣化をいかに防ぐかも重要なテーマであると指摘する。
「急速充電では負極の設計が鍵となります。リチウムが析出しにくい負極を開発することがポイントになります。現在のところ、充電時間の目標を10〜15分としています。試作品レベルでは3.5分での充電も可能ですが、本当にそこまで短縮する必要があるのかは市場の需要次第だと考えています。」
■AESCのロードマップ
AESCジャパンの今後のロードマップについて明石氏は、「現在は第5世代のバッテリーの量産を開始したところです。次の第6世代では、航続距離600km、第7世代で700〜800km、全固体電池では1000kmを目指しています」と明かす。
さらに、「長距離の航続性能だけでなく、5分間の急速充電で一定距離を走行できるバッテリーの開発にも取り組んでいます」とし、多様なニーズに応える技術開発を進めている。
また、バッテリーの役割は車両の駆動だけにとどまらない。「将来的には、EVバッテリーがオンデマンドで電力をグリッドに還元し、再生可能エネルギーの受け皿として機能するべきだと考えています」とは語る。
EV市場の成長とともに、バッテリー技術の進化は今後も続く。AESCジャパンは、「車載だけでなく、定置型エネルギー貯蔵を含め、あらゆる分野で使えるバッテリーの多様化を進めていきます」と締めくくった。
座学のあとは、座間工場の生産設備を見学することができた。
座間工場では、日産リーフやサクラ、三菱eKクロスEVやアウトランダー、ホンダN-VAN e: 向けの車載バッテリーを製造している。同社の相模原工場で製造されたロール形状の正極・負極から、セルを製造し、エイジングを経てバッテリーモジュールに組み上げるまでのプロセスを担当している。
一言に車載バッテリーと言っても、その生産プロセスは多くの工程に及ぶ。具体的には以下の通りだ。
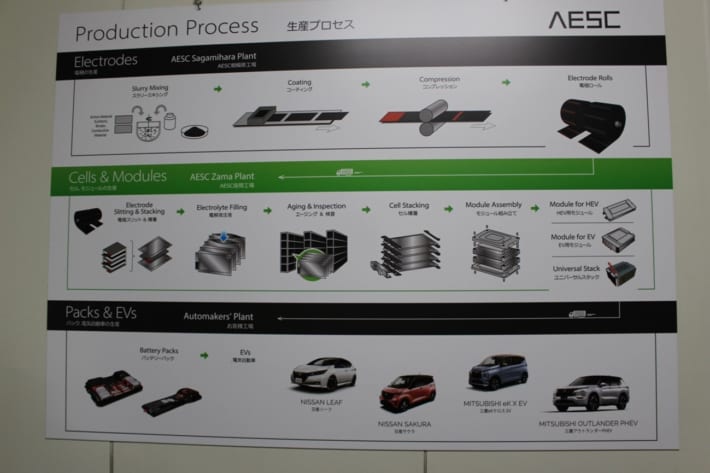
生産プロセス
- 正極・セパレーター・負極をバウチの大きさにカットする
- 正極・セパレーター・負極を積み重ね、セルの中身を製造
- セルをパウチに封入し、電解液を注入
- いちどセルを充電し、放電する過程で負極表面をコーティング
- 放電過程でコンタミ(ゴミ)の混入を検査し不良品を弾く
- 完成したセルを積み重ねてモジュールに組み立てて出荷
工場内に人影は少なく、整然と並んだ製造機械が粛々と稼働している印象だ。人間が介入する場面は、どちらかというと製造機械が問題なく動いているかどうか、不良品は出ていないか、異常な温度を発しているセルはないかなど、動作の確認をする役割を担っているようだ。
座間工場は、2010年に稼働開始したAESCジャパンの出自となる工場として、2.6GWhの生産能力を持ち、今後も本拠地として稼働を続けることになる。
また国内においては、2024年7月に稼働開始した茨城工場が、20GWhもの生産能力を持ち、最新世代のバッテリーを製造するマザー工場として大きな役割を果たすことになる。