電池は融通が効かない
だから開発も製造も大変
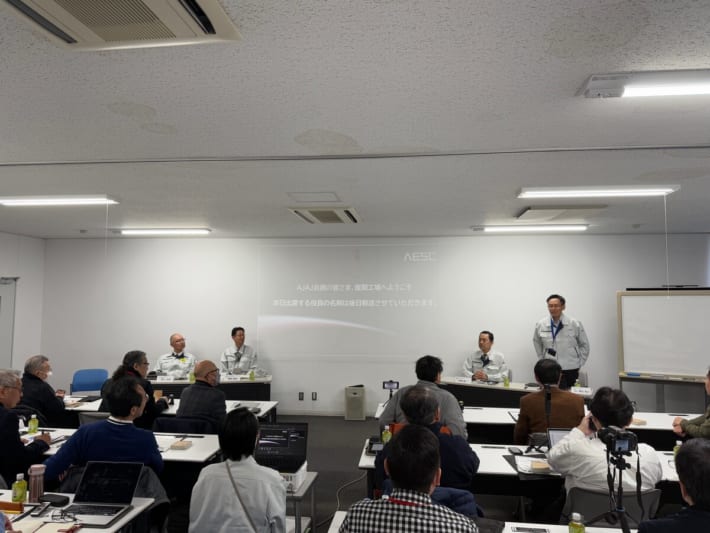
AESC(オートモーティブエナジーサプライ)は日産51%、NECトーキン49%の出資比率で2007年に設立された。自動車用動力電池を専門に製造する企業の誕生は、おそらく同社が初だっただろう。開発・製造のための拠点は日産自動車座間工場に置かれた。ここは昔、日産「サニー」など車両を製造していた。2010年以降は車載電池を作っている。「ICE(内燃機関)+変速機=パワートレーン」という式はいまも存在するが、「電池+電気モーター=パワートレーン」が仲間に加わった。その意味では、AESC座間工場はパワートレーン生産拠点である。
ここの製造設備は大掛かりであり、お金がかかっている。ずいぶん前に乾電池工場を取材したとき、「同じ仕様の製品を、無人で、延々と作り続けることが利益を産むカギ」と聞かされ、設備を見て納得した。巨大な装置産業である。
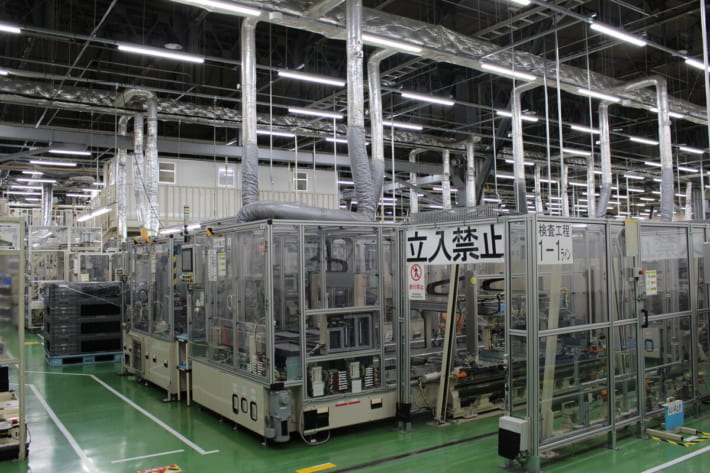
乾電池は円筒形だ。値段は安い。とくに日本は乾電池が安い。四角い9ボルト電池は値段が一気に高くなるが、おそらくその理由は9ボルトを稼ぐための原材料費だけでなく「設備費÷製造個数」の負担が上乗せされるためだろう。
一方、車載電池は「巻き=円筒型」がいいか、「折りたたみ=角型」がいいか、それとも「真っ平=ラミネート(パウチ)型」か。世の中にはこの3つが混在している。しかし、途中で注文を変えることはむずかしい。これと決めたらできる限りの数を作り、設備償却を早く終えることが求められる。
「まず、どんな電池が必要かをOEM(自動車メーカー)に訊く。そこで性能の相談をし、搭載要件を訊く。丸か、角か、平らか。どれがいいか。形状によって生産設備が変わるから、多くのOEMと取引しようと思ったら5〜6年先の電池の傾向を探る必要がある」
過去に取材して来た国内外の電池サプライヤーからはこう聞いている。いまでも変わらないのだろうか。AESCにも尋ねてみた。
「変わらないですよ。我われのラミネート電池にしても、縦×横の寸法が変わったら製造設備を変えないといけない。極材が変わっても同じ」
「電極がプラスとマイナスで別の側にあるのか、同じ側にあるのかでも製造工程の一部は決まってしまう」
AESCの動力電池は長い間、ラミネート型(パウチ型)セルだけだった。現在では角型セルも作っている。中国では定置用電池も作っている。2019年にAESCを買収した遠景集団(エンビジョングループ)は電池事業を持っていなかったが、現在はAESCの技術資産を使い電池分野のビジネスを加速させている。その中に定置用電池がある。その意味では「オートモーティブエナジー」という社名が、いささか古く感じる。
絶対に回答は得られないことを承知で「儲かりますか?」「赤字にはなりませんか?」と、松本昌一代表取締役社長兼CEOに尋ねた。
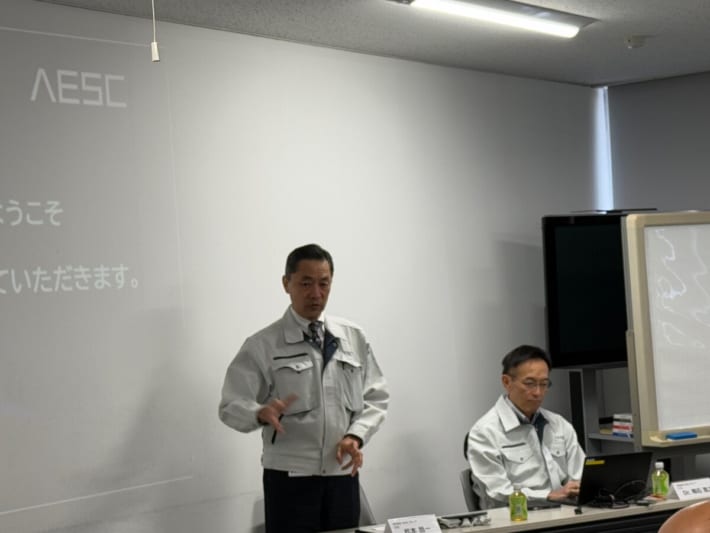
「量産立ち上げ当初から良品率を上げる目標をしっかりクリアしないとちゃんとした利益は出ない。工場建設はすべては先行投資。何年で回収できるかは工場ごとに違う」と回答してくれた。
裏を返せば「ちょっとへまをすればすぐ赤字」「OEMが発注量をちゃんと買い取ってくれず、クルマが売れないからと言って納品数を減らされれば赤字」「だからバッファーとして開発期間が短くて済む定置用電池も作る」ということなのだろうと思った次第。
さて、工場設備である。中国で見た(といってもほとんどの部分はビデオだけだったが)電池工場と大差ない。車載用の動力LIBを世界で初めて量産した会社がかつての日産・NEC合弁のAESCだから、当然、あちこちから見学にやってきて、いろいろと参考にされただろう。その意味ではAESC座間工場は世界の動力LIB工場のマザー工場と言っていい。
AESCの立ち上げに参加した役員氏は「この工場を作るときは温度・湿度に厳しい食品工場など、いろいろなところ見てまわって参考にした。食品製造工程は化学変化を待つ時間なので、品質管理のコンセプトが電池と似ている。クリーンに関する知見も似ている」と仰った。マザーより古い遠い親戚のグランドマザーがいたのだ。
電池製造工程を伺った。おもな構成部材は3つ。プラス(正極)側とマイナス(負極)側の「極材」と、これを隔てる「セパレーター」、電子(LIBの場合はイオン)の通り道となる「電解質」の3つ。これはNMC(ニッケル/マンガン/コバルト)系でもLFP(リン酸鉄)系でも、あるいはSSB(ソリッド・ステート・バッテリー=全固体電池)でも変わらない。
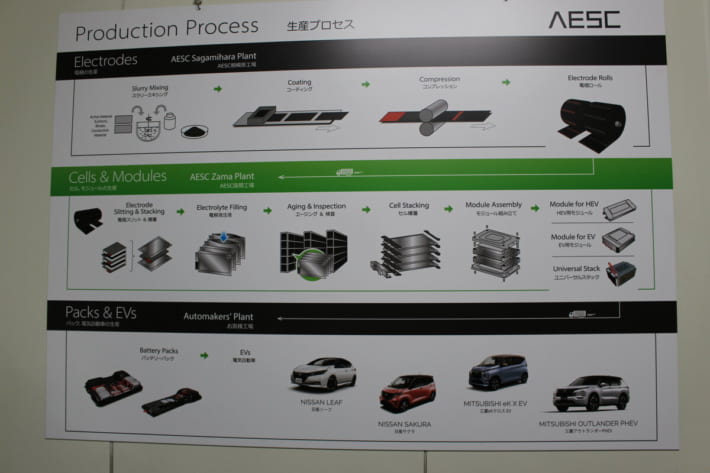
正極/負極のシートは近隣の相模原工場で作られ、幅2mほどの大きなマザーロールの状態で座間の電池製造ラインまで運ばれる。このマザーロールから、電池の寸法に合わせて切り出す。ロールケーキをナイフで切るように、長手方向に切り出す。この工程はスリッティングと呼ばれる。
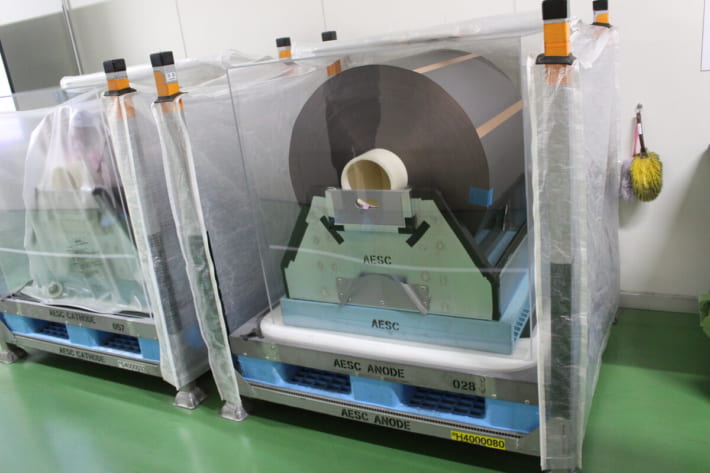
これが終わると、パウチ型の場合は「負極/セパレーター/正極」のセットをいくつも重ねる。AESCの現在の製品は、1セルの中に85枚が重なっているそうだ。展示見本ではいちばん上が黒っぽい色の負極だった。ということは、正極21枚と負極22枚、セパレーターが42枚なのかな。1枚ごとは何ミクロンという厚みでしかない。この、積み重ね工程はスタッキングと呼ばれ全自動で行われている。
スタッキングされた材料はレトルト食品のようにパウチされる。上下からアルミ薄皮ではさみ、まず3方を接合。この状態で真空室に入れられ、中に電解液を注入する。「気泡が入るのは絶対にNG」であり、だから真空中での作業になる。電解液は「ウェットティッシュのように液体が染み込んだ状態」になるくらい入れられ、すぐに密封。
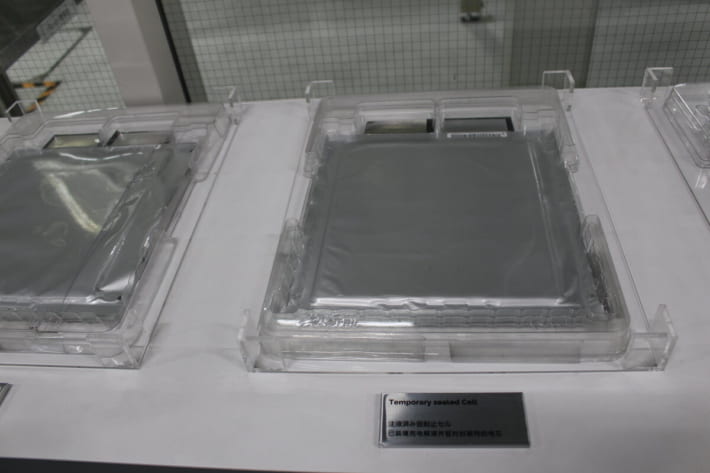
このあとがエージングと呼ばれる工程だ。出来上がったセルに電気を流す。
「初めて電気を流したとき、電解質液からジエチルカーボネイトというガスが発生する。電池内の気体を完全に抜くため、端っこに小さな穴を開けてガスを抜く」という儀式が、まず行われる。空気が入らないよう、この作業も真空室で行う。
そのあとはエージング室でじっくり寝かされる。
「電気を流すと、負極材と電解質が接する界面にSEI(ソリッド・エレクトロライト・インターフェーズ)と呼ばれる被膜が形成される。これを作ることがエージングの最大の目的。この皮膜は負極を保護しながらLiイオンの出入りを促し電解液の分解も抑制する」
もうひとつ、エージングの目的がある。
「万一、極材がこぼれ落ちたり金属ゴミが混入していたりすると、充電中に電解質液の中に溶け出す。これがブリッジになり、セパレーターを突き破る。これがマイクロショートという現象。ごく小さな突き破りでも、電圧低下が大きく出るので、充放電を監視しているとマイクロショートが発生したかどうか検知できる。これをスクリーニングする」
エージングにかかる時間は2週間以上だという。出荷前の電池にとって、これは準備体操だろうか。
いや、教育工程というほうがいい。よく「電池はナマモノ」と言われるが、「それはやがて朽ち果てて腐って使い物にならなくなるから」だけではない。AESC座間工場が食品工場などの環境管理を参考にしたように、電池セルに電気を通してエージングする工程は、レトルト食品のカレーやシチューで言えば「全数味見工程」だ。セルの設計値どおりの性能に仕上がっているか、電気を流して「カラ」から「満充電」までゆっくり充電し、その逆の放電もやる。2週間かけて味見をして、OKのものだけ出荷する。まさにナマモノだ。
以前、私は市販の小さな薄型パウチLIBに個人的釘刺し試験をしたことがある。まったくアホだった。耐火手袋とゴーグルをして。電池を万力に固定して、少し離れたところからこわごわ釘を刺したら電池に逆襲され、露出していた前髪がごそっと焦げた。それ以来、ノートパソコンや家電製品のLIBはていねいに扱っている。
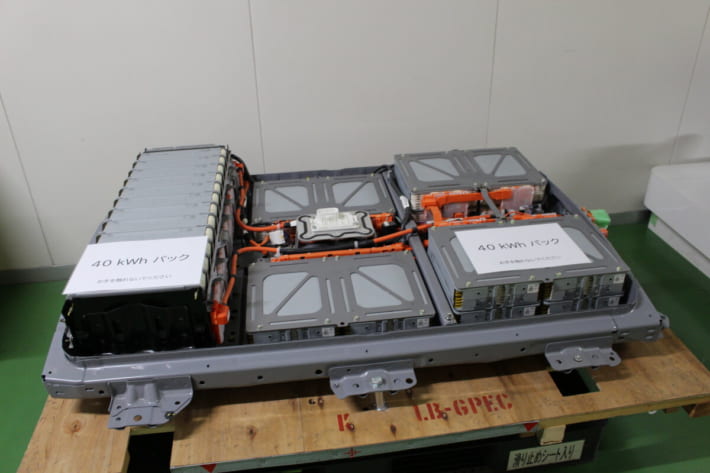
その一件を思い出すと、2万チャンネルも使って計測できるBEV何十台ぶんものLIBセルをエージングするエージング室は、弾薬庫並みのエネルギー量だ。しかし、工場での事故も製品としてBEVに積まれてからも、AESCのLIBは一度も発火事故を起こしていないのだから、日本の「ものづくり」は緻密で安全でスゴいと思う。
工場内にはほとんど人がいない。機械だけが黙々と働く、ただし、工場内のあちこちを監視している集中管理室には人がいた。セル製造工程は全自動なので、この管理室で工場内を監視し、生産管理と設備の状態管理を行なっている。同時に工場内の温度と湿度を管理する。温度が変わると電池容量が変わってしまうので同じ検査ができなくなる。ああ、ここも食品工場を連想させる。
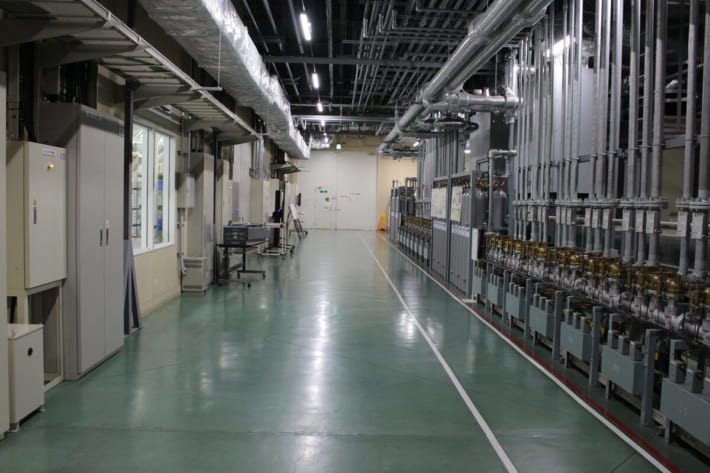
検査工程にも人がいた。外観検査にはカメラ画像とAIを使い、バスバーのレーザー接合も自動で行なうが、最終的には人の目による検査が行われていた。最後に、すべてのセルに2次元バーコードが刻印される。このコードは製造工程のあらゆるデータと紐付けられていて、その数は1セルで45万。
材料搬入から電池出荷までは約1か月。自動車のボディ溶接〜塗装〜最終組み立ては3日ほどで終わるから、それに比べて電池はなんと手間のかかることか。利益率は低いだろう。まったくの個人的予想で、水道高熱費、人件費、施設償却費を加えた製造原価率98%。
最後にまったくの余談を。
まだバッテリーパック取り外しができたころのi-Book用バッテリーパックを中国・北京で買った。ちゃんとしたアップル・ストア=林檎商店だった。ところが、そのバッテリーパックは突然、ボン!と破裂した。i-Bookはぐにゃっと曲がって使い物にならなくなった。
東京のサービスセンターに持ち込んだら「このバッテリーパックは正規品ではありません」と言われた。そんなはずはないですよ、ちゃんと林檎商店で買いましたから……。
ところが、調べてもらったら、その林檎商店がニセ物だった。これは私が釘刺し試験で殺した電池のたたりだったのか、それとも物見遊山で入ってさんざんバカにした「ニセ上海モーターショー」の怨念だったのか。
■参加者(敬称略、五十音順) |
---|
有元正存/石川真禧照/大谷達也/大音安弘/岡崎五朗/片岡英明/桂伸一/日下部保雄/工藤貴宏/菰田潔/佐藤耕一/鈴木直也/塩見智/高橋明/高根英幸/ 高山正寛/近田茂/中村孝仁/南陽一浩/西川昇吾/萩原文博/ピーター・ライオン/牧野茂雄/松田秀士/桃田健史/森川オサム/諸星陽一/山崎明/山崎元裕/吉田由美 |